Now I have the requirements for the control ranges I need its time to get down to the nitty-gritty and get a DAC up and running so we can make some measurements. The maximum dynamic range I need for this project is 6000 individual steps – this was identified in the calculations for the voltage control for the 0-6V rage in Part 5, so let us start there.
There are many options for DAC’s to choose from, I want to keep the cost and component count down so my starting point is a low-cost single component solution from Microchip, part number MCP4822. This is a dual 12-bit DAC with two channels and a built-in voltage reference. I get independent voltage and current control from one 8-pin chip – wow! However, there is a problem with this part, it only has 12-bit resolution which will only give me 4096 individual steps and my design calls for 6000. The problem with choosing components with a higher number of bits is that they start to get expensive. I want to see if it’s possible to extend the range of the DAC using software and a technique called “dithering” or “modulation”.
The idea here is pretty simple, to increase the resolution of the DAC you can continuously switch the output between two or more codes, feed the result into a low-pass filter and get the average voltage. If you switch between two adjacent codes with a variable mark space ratio like you do in PWM, it should be possible to extend the range of the DAC without creating large ripples on the voltage head making the low pass filter easy to construct. That is the theory at least, I need to try it and see what the results are in practice.
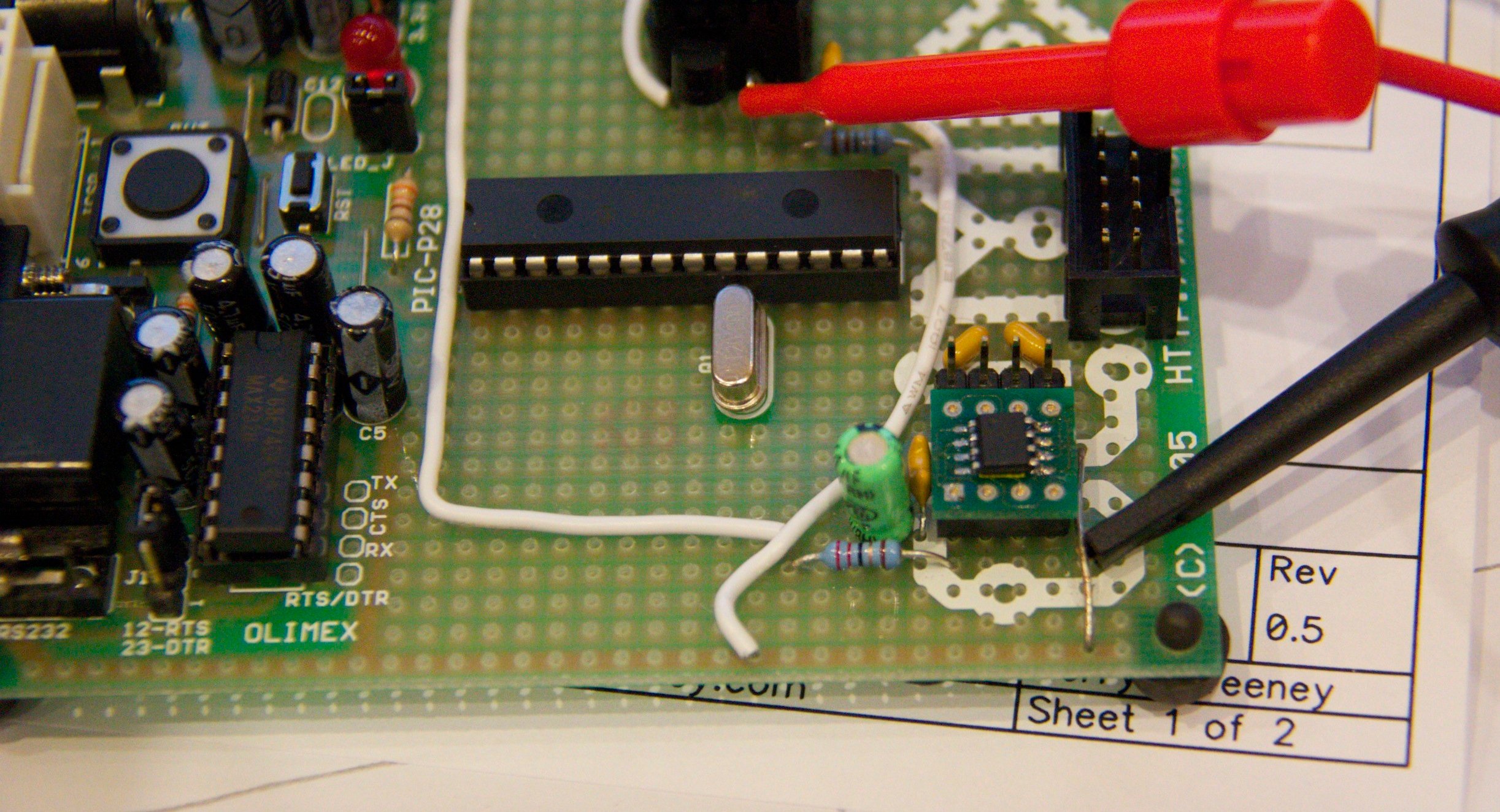
Before getting too complicated though, I thought it would be good to run the DAC in static mode, set some codes and measure what we get. The DAC has 4096 steps, the internal reference voltage is 2.048v and the chip has a x2 gain option so I should be able to program any voltage between 0v and 4.096v in 1mV steps by simply programming a digital code between 0 and 4096 into the DAC channel. To get this up and running I hooked up a PIC micro controller, the DAC chip and an RS232 serial interface. The firmware in the PIC will allow me to interact with the DAC through a simple serial terminal on my computer.
Before any MPS430, Atmel or Arduino die-hard fans start giving me advice on micro controller choice — forget it. They are all good parts, I just happen to personally like PIC’s because I know them and I have the tools and a whole bunch of them sitting here to play with – if you are not happy with my choice of micro controller thats tough…. I am not going to change it or enter into any debate over the pro’s and cons of other devices – I am sticking with PIC’s for this one and if you try to change my mind I will ignore you – sorry.
Here is the schematic diagram for the prototype I am using.
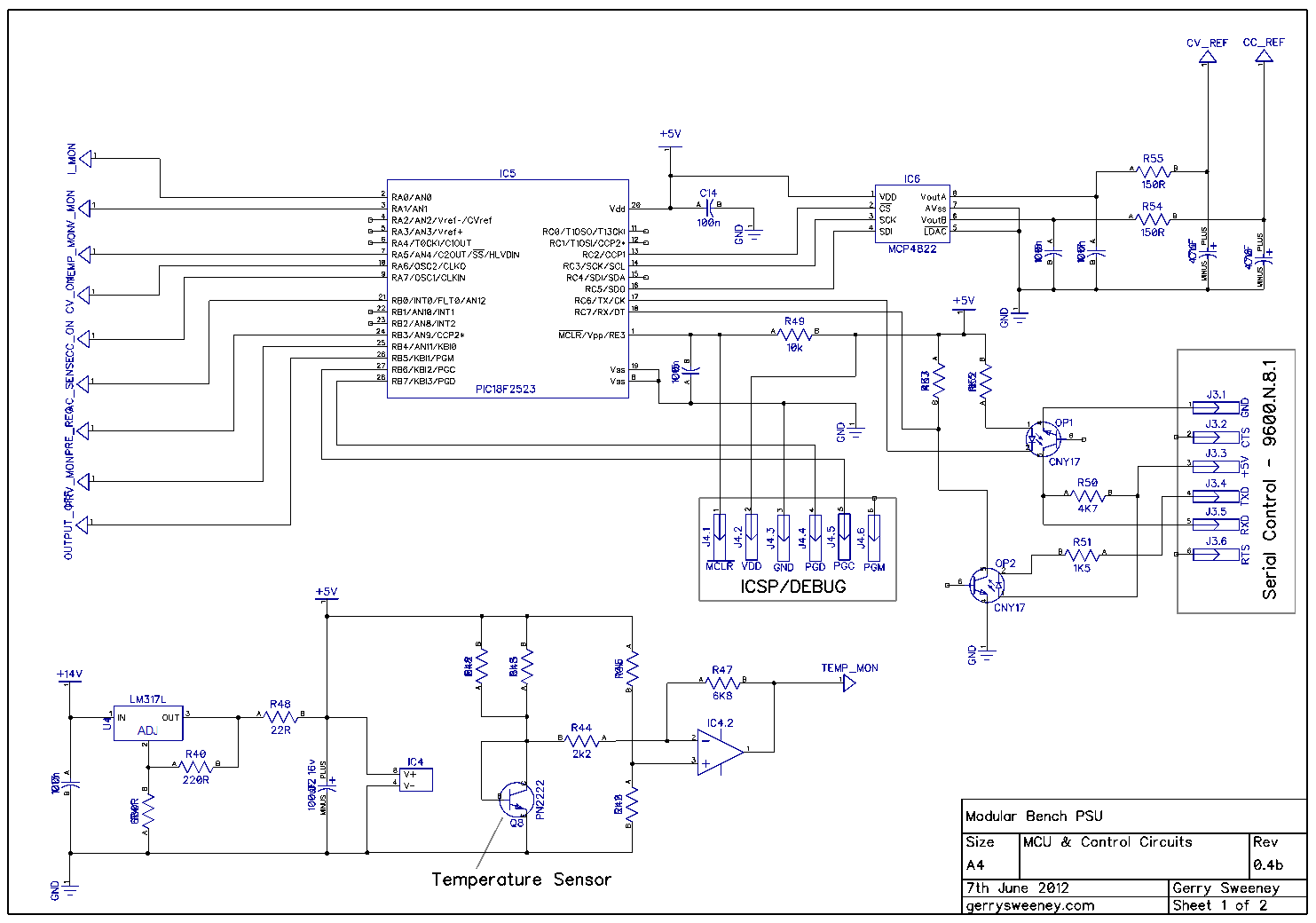
For the dithering I have decided to extend the DAC by 2 bits. Extending by two bits means I have to write a sequence of four codes continuously in succession to the DAC. I am writing approximately 1000 codes per second within a timer driven high-priority interrupt routine which ensures that the timing remains constant. Timing errors will introduce more DNL errors so the code stream needs to be constant and accurate. The codes written are the base code value followed by the base code value + 1. The two least significant bits from the now 14-bit word controls how many times each of the two values is written. For example, to get four steps between code 100 and code 101 we would write the following codes: –
100.00 100 100 100 100
100.25 100 100 100 101
100.5 100 100 101 101
100.75 100 101 101 101
Extending by 3 bits is an option and would mean I have to write a sequence of eight codes, again following the same explanation as above, here are the codes that would be written
100.00 100 100 100 100 100 100 100 100
100.125 100 100 100 100 100 100 100 101
100.250 100 100 100 100 100 100 101 101
100.375 100 100 100 100 100 101 101 101
100.500 100 100 100 100 101 101 101 101
100.625 100 100 100 101 101 101 101 101
100.750 100 100 101 101 101 101 101 101
100.875 100 101 101 101 101 101 101 101
I tried the three bits as an academic exercise but I have decided not to go to three bits because of the noise, ripple and integral errors generated. The cost of the filter circuitry and the expansion of the line items in the bill of materials would probably outweigh the cost of upgrading the DAC component to a higher resolution part.
I have selected a number of spot voltages in the range to benchmark what I get from the DAC. The following table sets out the results I measured. (I am using a calibrated HP 34401A meter for all measurements).
Spot Voltage |
DAC Code |
Measured MCP4822 (12bit static) |
Error |
DAC Code |
Measured MCP4822 (14bit dith) |
Error |
0 |
0 |
0.0015V |
+0.0015V |
0 |
0.0014V |
+0.0014V |
0.001V |
1 |
0.0015V |
+0.0015V |
4 |
0.0016V |
+0.0002V |
0.002V |
2 |
0.0024V |
+0.0014V |
8 |
0.0026V |
+0.0006V |
0.003V |
3 |
0.0034V |
+0.0004V |
12 |
0.0036V |
+0.0006V |
0.004V |
4 |
0.0044V |
+0.0004V |
16 |
0.0046V |
+0.0006V |
100mv |
100 |
0.1024V |
+0.0024V |
400 |
0.1026V |
+0.0026V |
500mv |
500 |
0.5024v |
+0.0024 |
2000 |
0.5026V |
+0.0026V |
501mv |
501 |
0.5034v |
+0.0024 |
2004 |
0.5036V |
+0.0026V |
1V |
1000 |
1.0004V |
+0.0004V |
4000 |
1.0006V |
+0.0006V |
1.5V |
1500 |
1.4975 |
-0.0025 |
6000 |
1.4977V |
-0.0023V |
2.5V |
2500 |
2.5014 |
+0.0014 |
10000 |
2.5016V |
+0.0016V |
3V |
3000 |
2.9993 |
-0.0007 |
12000 |
2.9995V |
-0.0005V |
3.001V |
3001 |
3.0002 |
+0.0002 |
12004 |
3.0005V |
+0.0005V |
3.002V |
3002 |
3.0012 |
-0.0008 |
12008 |
3.0014V |
+0.0006V |
3.9v |
3900 |
3.8968 |
-0.0032 |
15600 |
3.8969V |
-0.0031V |
4.095v |
4095 |
4.0916 |
-0.0034 |
16379 |
4.0916V |
-0.0034V |
Well, that is disappointing given I am aiming for a precision of 1mV and to get a control voltage of 0-6V I need accurate 500µV steps. So whats wrong here? Having read the data sheet there are some gotcha’s that naively you might ignore as I did. Every DAC has two really important parameters called Integral Non-linearity (INL) and Differential Non-Linearity (DNL). The DNL defines the maximum deviation to expect from the “ideal” voltage for any given code, expressed in LSB’s (or counts from ideal) and INL is the accumulated DNL errors that occur over the whole range. Fundamentally, the DAC is based on a resistor string network and its not easy to make highly accurate resistors, as soon as you start needing more accuracy the cost of the part rises very steeply, and even with the best part money can buy there will still be errors. The more bits you extend the DAC by using dithering, the more error you introduce and the more noise you introduce too. While extending by two bits is probably acceptable with a decent low-pass filter, extending by three bits and beyond is not really practical. As an aside, the noise figures for the MCP4x22 parts are not that great – something one must consider when the reference voltage generated is going to be amplified, the noise will also be amplified.
In summary then, I want accuracy and precision but I want reasonable cost and even if I spend a lot of money I will still have errors. The lesson learned for me is I now no longer think of a DAC as an accurate programmable voltage source – it’s not, it is a close approximation only. The MCP4922 (MCP4822) is a nice part for the $$$ and useful for some things I have no doubt, but it’s not good enough for what I want to achieve in this project. Even with the resolution extension to 14-bits it falls short. Actually to be fair, even with the errors in the DAC this would be make a pretty good degree of control, it is probably more accurate than most of the lower end bench PSU’s out there, but my benchmark is the Agilent E3631A so I need to achieve much better than this. The MCP4x22 device is the best resolution DAC Microchip do so I must now search for other parts instead – Linear Technologies and Analog Devices are the logical starting point for my search.
There is one further possibility which I have yet to try, which is to combine both 12-bit DAC outputs to create a much higher resolution DAC, the block diagram for such a solution is shown in the data sheet for the part. This is well worth a look because if it works well enough, the cost of the two chips may well still be cheaper than an upgraded DAC part. I will build this out at some point and give it a try.
This project also needs to implement metering in order to monitor the output volts and current drawn by the load connected to the PSU, and this needs to be reasonably accurate to 1mV too, that’s 5-digits I need which in its self is a tall order. However, it occurred to me that if I could get an ADC that was accurate enough and a DAC with enough resolution to provide headroom for trimming it might be possible to build a self-calibrating system that trims the DAC output to match the desired programmed voltage each time you set a new voltage. That is what I will look at in Part 8.